This spring, we installed two GI-275 Electronic Flight Instruments in the Bellanca, replacing the vacuum-powered attitude indicator, the vacuum-powered directional gyro, and the GTN-650’s CDI. The GI-275 is round, steam-gauge form factor electronic flight instrument that can present attitude indicator, horizontal situation indicator, course deviation indicator, moving map, or engine instrumentation pages, depending on how it is installed and used. Importantly, unlike the cheaper G5 Electronic Flight Instrument, the GI-275 can provide attitude source data for the Century IIb autopilot that is installed in the Bellanca, so I was able to remove the vacuum attitude indicator. While I could have removed the altimeter, airspeed, and backup attitude indicator, I chose to leave them for now, to have an extra level of redundancy. I did remove the vertical speed indicator, both because it is not really needed in an emergency situation and because the existing VSI desperately needed to be overhauled. The new panel configuration is pictured below (taken during annual, so the kick panels and carpet are not installed):
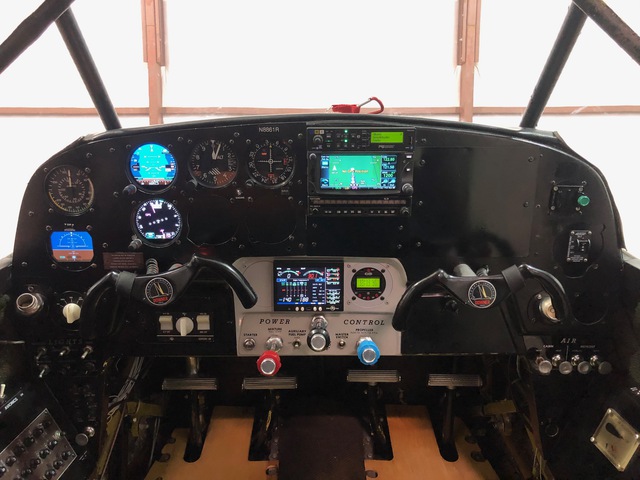
The HSI can display GPS or VOR/LOC input from the GTN 650 or VOR/LOC input from the SL30, including bearing pointers from any of the three sources. Because both 275s replaced primary instruments, they can only present a subset of the pages that the 275 generally supports. The top 275 can only display the ADI page (although that includes CDI indicators) and the bottom 275 can only display the ADI, HSI, and “HSI Map” page.
The big win in all the updates is that I no longer need a vacuum system. The vacuum pump, regulator, filter, pressure gauge, and hoses all came out, saving 7 lbs. I’ve had 3 gyro failures in 12 years, and dry vacuum pumps are notorious for total failure without warning, so the increase in reliability should be a real win.
Functionality Gained
The biggest functional gain is the switch from DG + CDI to an HSI, which presents two instrument’s worth of information in one instrument. The ADI can display airspeed, altitude, heading, and navigation deviation, which means that it can be the sole instrument needed for navigation in instrument conditions, meaning that there’s less of an instrument scan and more of an instrument focus point. The altitude and (optionally, although I don’t have it turned on) airspeed bugs are nice for quickly checking whether or not you are pointed in the right direction. Of course, I could have gotten some of this functionality replacing the DG and CDI with a vacuum HSI.
The biggest gain in functionality is the integration between the 275s and the GTN650. The 275s provide heading and baro-corrected altitude to the 650, so that it can auto-sequence heading and altitude waypoints, which are common on departure and missed approach procedures. The HSI page displays next waypoint and distance to next waypoint information, which saves space on the 650 from displaying those fields. Finally, the 275 acts as a GPS Steering driver for the Century IIb autopilot. GPS Steering (GPSS) allows the GPS to compute smooth turns to intercept new courses, based on airspeed and winds, with significantly less wandering and overshooting of sharp turns that the traditional nav input. Modern autopilots can take GPSS inputs directly from the GPS, but for older autopilots, the solution is to have an emulator box (or the 275 in this case) drive heading inputs.
Complaints
There are a couple of things I don’t like about the 275s. There’s an altitude trend indicator (where you will be in 30 seconds) and a numerical vertical speed indicator, but, unlike the larger Garmin electronic flight instruments, there is no visual vertical speed indicator. I didn’t think I would miss it and, most of the time, I don’t. However, on a recent VOR approach, it really would have been nice to have a visual VSI. When there’s glide slope information available (like a precision approach or when the 650 can generate a descent profile), it is not a huge problem, but in the situations where the 650 cannot generate an descent profile (either too steep of an approach or a VOR approach from FAF to MAP), then it is a bit of a pain.
The switch between GPSS and Heading mode for driving the autopilot is three levels deep in the menu system on the 275. In an approach environment, it is pretty common to have to switch between vectors (ie, heading mode) and own navigation (ie, gpss) fairly quickly. Garmin’s latest software version has apparently fixed this and enabled an external switch, which makes for very rapid and positive switching between the two modes.
I’ve run into trouble activating the synthetic vision functionality on the ADI (a $500 add-on). The synthetic vision itself doesn’t seem all that useful, based on the 10 hour free trial. However, the flight path marker feature is really nice for maintaining level flight in IFR, and the traffic display for converging targets is nice as well. Apparently, my problems are not unique and Garmin has been working with me to fix the issue. The next step is yet another trip to the local Garmin dealer, but at least this time, it appears it will be on Garmin’s dime.
Redundancy / Regrets
I do have a couple of regrets on how the avionics shop and I agreed to do the installation. I chose not to install the temperature probe, the panel-mount USB port, or the VFR backup GPS antenna. I should have installed all three (although I lucked out a bit on the USB ports). Because I retained the airspeed, altimeter, and backup AI, the system was not required to have a revisionary switch, which I probably should have just had them install, to future proof the installation by allowing me to remove the remaining steam gauges.
Garmin’s high speed data bus (HSDB) connectivity is used to connect the 275s and the GTN650 GPS. Despite the 650 having plenty of HSDB ports, the 275 installation manual requires that the 650 connect to the ADI and then the ADI connect to the HSI. This means if the ADI completely fails, then the HSI unit does not have connectivity to a GPS source. The magnetometer also has to be wired to the ADI, due to some issue with the autopilot integration (this was the source of many calls between the shop and Garmin), because logical thought suggests the magnetometer should be hooked up to the HSI and the manual is very unclear on the point), which means that if the ADI completely fails, the HSI unit also does not have heading indication. It does have an internal ADAHRS unit, so I’ll know which way is up, how high I am, and how fast I’m going, but I won’t know which way I’m going. The best solution appears to be connecting the glare-shield VFR-only WAAS GPS antenna to the HSI unit. Then, if the ADI unit fails, I will still lose connectivity between the GTN650 and the HSI and still lose the magnetometer, but the HSI unit will be able to build its own ground track, which is good enough in an emergency. If the HSI completely fails, the ADI can still talk to the GTN650 and display course deviation indicators and heading, so I’m good there as well.
The temperature probe is optional in my install, because the existing RC Allen RCA2610 attitude indicator includes a rate of turn indicator. But to remove the 2610, I would have to add the temperature probe so that the 275 can generate standard rate of turn indicators on the ADI. The only real challenge is finding a mounting location that is in the approved lightening zone, not in the sun when in level flight, and not in the exhaust stream. It looks like the wing inspection cover to inspect the rear spar attach bolts might be the best option. Not a huge hurry, but probably would have been simpler to have this done at the start.
Finally, the panel-mount USB charger ports do not add any features, but, in addition to providing USB device power from ship’s power, they provide a USB data port to the GI-275. Rather than having to blindly reach behind the panel to find the USB port for database upgrades, I could plug a USB drive into the panel mount port and be good to go. At some point, I will have the cigarette lighter replaced with the USB port, if nothing else, to remove the cigarette lighter.
Conclusions
Despite the little complaints, I’m really happy with the improvements for flying IFR. The 275s are definitely more complex than the vacuum instruments they replaced, but the improvement in flying in IFR conditions is incredible. The altitude bug (with audible deviation beeps), minimums callout, and the greatly simplified scan all make flying IFR more enjoyable. With a couple of software improvements in the works, I think I’m going to be even happier with the panel upgrades. I do wish that Garmin would add support for flight plan transfer between the 275’s Connext bluetooth interface and the GTN650. If that existed, I could remove the FlightStream 210 and have one fewer box in the airplane.
While the shop was installing the flight instruments, I also had them replace the Narco AT-150 transponder and the GDL-88 ADS-b in/out boxes with the Garmin GTX345r remote ADS-b transponder. In addition to allowing me to gain some useful load and remove the 18,000′ altitude restriction, it also frees up some much needed panel space, as the 345r is controlled by the GTN650 display.